What Is Alloy 20 Pipe Used For?
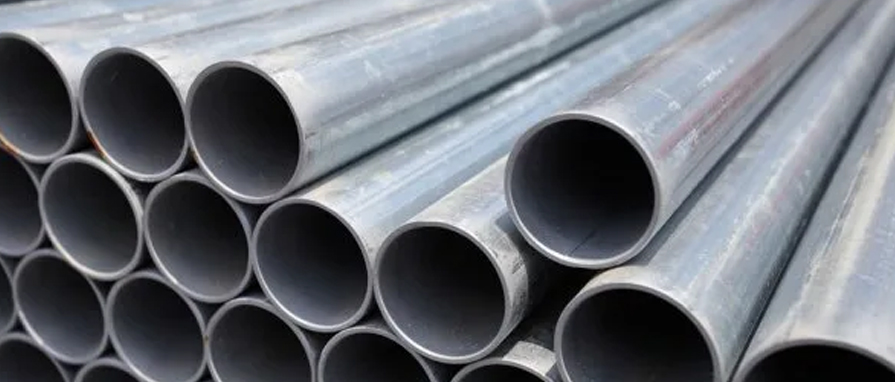
Alloy 20 is an austenitic chromium-iron-nickel alloy with exceptional corrosion resistance in chemical conditions. It comprises sulfuric acid as well as a variety of hostile media. Niobium stabilizes the alloy, making it more resistant to intergranular corrosion. Because it outperforms conventional stainless steel, Alloy 20 can assist deliver possible cost savings when compared to higher nickel-based alloys.
Additional Information About Alloy 20 Pipe:
Alloy 20, also known as UNS N08020, is a high alloy pipe composed of a special stainless steel grade that has good resistance to stress corrosion cracking in chloride and sulfuric acid. Copper component in the alloy aids in delivering great general corrosion resistance. The stainless steel alloy is commonly used for pickling equipment, process pipes, heat exchangers, and manufacturing tanks due to its resistance to pitting, crevice corrosion, and corrosion.
Alloy 20 Fittings Key Characteristics
Mechanical qualities that are exceptional
Fabrication-friendly material
Resistance to other acids, such as nitric and phosphoric acids, is outstanding.
Strong stress corrosion resistance - cracking in boiling 20 to 40% sulfuric acid
Pitting, crevice corrosion, and corrosion resistance
Alloy 20 Pipe Uses:
Applications & Industries:
Food processing, pharmaceuticals, maritime, petrochemical, refining, and chemical processing are just a few of the sectors that employ Alloy 20. Pumps and valves, fasteners, food processing equipment, fittings, agitators, mixing tanks, and storage tanks are among the applications' ultimate uses.
According to ASME, applications are limited to a maximum temperature of 1000°F. It's also crucial to figure out if you'll be able to accomplish the required corrosion resistance in the particular environment.
Resistance to Corrosion:
Sulfuric acid resistance is excellent in Alloy 20. It also exhibits appropriate resistance to aqueous salt solution, nitric acid, and phosphoric acid. If chloride stress corrosion cracking is an issue, Alloy 20 has a great solution. The reason for this is because it aids in the resistance of crevice and pitting, resulting in increased durability. When dealing with chloride ions, you must exercise caution since the rate of corrosion can rapidly rise over time.
Fabrication and Heat Treatment:
Traditional cold-work and hot-work procedures can be used to manufacture Alloy 20. Heating hot forged material between 2100°F and 2250°F with precise temperature control is required. It also guarantees that the material does not cool below 1800 degrees Fahrenheit before being forged. After hot working, anneal the materials by heating them to 1725°F or 1850°F for at least 30 minutes per inch of thickness, then quenching them in water.
When stress relief is required, lower the temperature to below 1000°F and follow with a water quench. It can happen when a specified temperature has been achieved for the necessary amount of time. Alloy 20 must be annealed at a temperature of 1725°F to 1850°F for 30 minutes per inch of thickness. Heat the alloy to 2100°F to reduce the hardness, however this may compromise the alloy's stability.
Navpad Steel Centre is a top manufacturer & exporter of Alloy 20 Pipes. If you have any requirement contact us today.